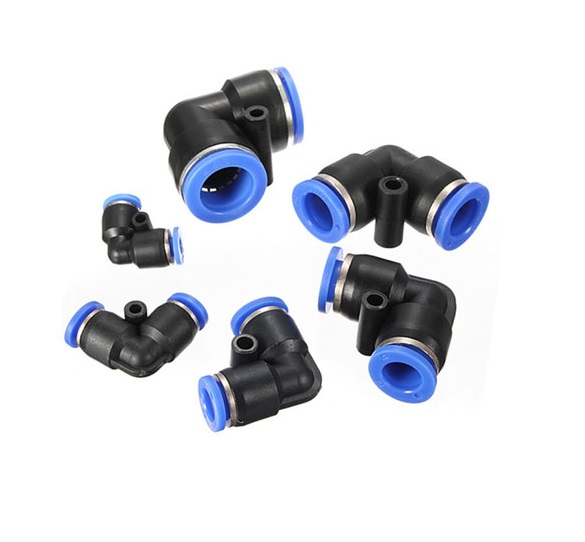
Pneumatic is one of the types of energy that is currently widely used in industry and it can be said that today there are few factories or industrial centers that do not use the pneumatic system and in this century is one of the proven types of energy It is the human being who relies on it to walk the path of industry.
Pneumonia in Greek means wind breathing and pneumatics is a science that talks about the movements and events of the air. Today, pneumatics is known among the industrialists as a very clean, low-risk and cheap energy, and it is widely used due to its advantages and properties such as high efficiency, controllability and ease of maintenance.
With the development of hydraulics and electronics and their increasing use in industry, control systems have evolved into modern and advanced systems such as pneumatic systems. Pneumatic or pneumatic systems are used in cases where relatively low forces (about one ton) and high movement speeds are required (such as systems used in robot actuators).
If the applications of hydraulic systems are more in cases where high powers and precisely controlled speeds are desired (such as hydraulic jacks, brakes and hydraulic steering). The advantages of a pneumatic or pneumatic system over other mechanical and electrical systems include the following:
simple design
Ability to increase power
Simplicity and accuracy of control
flexibility
high efficiency
Assurance
The pneumatic system has fewer actuators than other mechanical systems and can achieve linear or rotational movements with high power and proper control at any point, because the transmission of power by the flow of high pressure fluid in the transmission lines (pipes and Hoses) but in other mechanical systems, components such as cams, gears, steering, levers, clutches and… are used to transmit power.
The use of flexible hoses transforms pneumatic and hydraulic systems into flexible systems in which there are no space constraints for the installation of other systems.
Hydraulic and pneumatic systems have high efficiency due to low friction and low cost. In addition, by using safety valves and pressure and heat switches, a system resistant to sudden loads, heat or excessive pressure can be built, which shows the high reliability of these systems. The pneumatic system is used in the oil and petrochemical, paper, steel, aerospace and dental industries.
To transfer power to a pressurized fluid (compressible or incompressible), we need to convert mechanical force into compressed fluid power in hydraulic systems by hydraulic pumps. The next step is to transfer the force to the desired point, which is done by pipes, hoses and clamps. After the pressure is controlled and the flow direction is determined by the valves, the pressurized fluid is directed to the actuators (cylinders or hydraulic motors) to convert the fluid power into the required mechanical force (linear or rotational).
Pneumatic components are designed for working pressures up to 800 to 1000 kPa (8-10 bar). Experience shows that for optimal performance, a pressure of approximately 600 kPa (6 bar) is suitable, and a pressure drop of about 10 to 5 kPa (0.1-1.5 bar) is always expected in the system due to the presence of paths. Elbow block is a leak and pressure drop in the pipes, which depends on the size of the piping system and how it is designed.